YAZARLAR
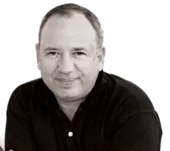
Henry Ford, üretim maliyetlerini düşürecek fikri, yani bant üretimini, 1913 yılının Aralık ayında tam anlamıyla hayata geçirdi. Böylece 1 otomobil üretmek için harcanan zaman 12 saatten 2.30 saate düşerken, maliyeti de aşağı çekerek ortalama gelire sahip ABD'li ailelere otomobil sahibi olma fırsatı tanıyordu. Bu yöntem sayesinde Ford, tüm sektöre büyüme şansı verirken otomobilin yaygınlaşmasında liderlik rolünü kazanmış oldu. Büyük adetlerde seri üretim yapmak isteyen otomobil fi rmaları bant üretimi tekniğini kullanmaya başladıktan sonra rekabet de iyice kızışmaya başladı. Maliyetleri düşürmek gerekliydi ama kaliteden de ödün verilmemeliydi. 1950'li yıllarda Japonya'da seri üretim için yepyeni bir yaklaşım doğdu. Toyota mühendisleri tarafından geliştirilen Kaizen sisteminde yalın üretim teknikleri devreye girdi. Yalın üretimde, üretim süreçlerindeki maliyet artırıcı etkenler törpülendi ya da değiştirildi. Örneğin stok kontrolü ve maliyetini aşmak için üretimde kullanılacak parçaların, üretim günü fabrikaya gelmesi sağlandı.
Üretim süreçlerinin maliyet açısından daha da iyileştirilmesi robotlar sayesinde artık son noktaya oldukça yaklaştı. Bu yüzden otomobil üreticileri farklı alanlara yöneldi. Örneğin ortak platform stratejisi. Özellikle çok markalı gruplarda her markanın her modelinin ayrı platformlara sahip olması üretim ve geliştirme maliyetlerini çok yükselten bir etken. Bu sorunu şemsiyesi altındaki farklı markaların aynı sınıft aki modellerini ortak platform üzerinde üretme konusunda en ciddi adımları VW Grubu atmıştı. VW Golf platformu üzerinde yükselen Skoda Octavia, Seat Leon, Audi A3 gibi modellerle grup geliştirme maliyetlerini yaklaşık yüzde 20 oranında ve süresini de yaklaşık yüzde 30 oranında aşağı çekerken, aynı parçadan çok daha fazla üretilmesi sonucu üretim maliyetlerini aşağı çekmeyi başardı. Grubun 2012'de tanıttığı yeni modüler platformu olan MQB sayesinde farklı aks mesafelerine, iz açıklıklarına, koltuk yapısına göre 40'tan fazla farklı otomobil geliştirilebiliyor. Dört temel bölümden oluşan MQB'de ön aks bölümü tüm modellerde aynı kalırken, burun, yaşam kabini ve arka bölüm değiştirilebiliyor. Böylece mini sınıft an lüks sedana kadar farklı sınıfl arda otomobiller aynı üretim bandından çıkabiliyor. Üstelik motor yerleşimlerinin de MQB kullanan tüm modellerde standart hale gelmesiyle VW Grubu motor-şanzıman çeşitliliğini yüzde 90 oranında azaltabiliyor. Grup, 2014 yılında yaklaşık 2 milyon adet MQB otomobil üretmiş olacak. Bu rakam 2016'da 4 milyon, 2020 yılında da 6 milyon adede ulaşacak. Bu da grup içerisinde otomobil başına düşen Ar-Ge ve üretim maliyetlerinin ciddi oranda düşmesi anlamına geliyor, Elbette VW Grubu'nu izleyen başka devler de var. Örneğin Renault-Nissan Alliance, Fiat Chrysler Group ve PSA gibi. Renault-Nissan, mini, küçük ve kompakt sınıft a üç ortak modüler platform kullanımıyla tedarikte yüzde 30, mühendislik giderlerinde yüzde 40 avantaj sağlayacağını açıklıyor. Fiat Chrysler de üç ortak platformla 1,5 milyar Euro tasarruf edeceğini söylerken, PSA Grubu (Peugeot ve Citroen) 2022 yılına kadar 7 olan platform sayısını 2'ye düşürmek için çalışıyor. Peki, aynı şemsiye altındaki markaların farklı modellerinde aynı altyapıyı kullanmanın riski yok mu? İşte burada devasa boyutlarda geri çağırma operasyonları karşımıza çıkıyor. Seri üretimde gözden kaçabilecek hatalı üretilmiş bir parça milyonlarca aracın geri çağrılmasına sebep olabilir. Böyle bir operasyonun maliyeti, otomobil devlerini bile zora sokabilecek kadar yüksek olabilir. Üstelik gittikçe daha fazla elektronik sisteme sahip olan otomobillerde problem çıkma olasılığı da yükseliyor. Tabii bir diğer konu da aynı platforma, yani aynı motor ve şanzımana, aynı elektronik alt yapıya, aynı süspansiyon sistemine sahip iki otomobilden birinin neredeyse yüzde 50 daha pahalı olmasını açıklamak da daha zor olmaya başlayacak. Tasarım, imaj ve plastik kalitesi bu farklı açıklamaya nereye kadar etkili olur göreceğiz…
- Kış Lastiği Zamanı Geldi Havalar soğuyor, yağışlar artıyor. Doğu bölgelerimizden ve yüksek kesimlerden kar yağışı haberleri gelmeye başladı. Tüm bu gelişmeler otomobil ve ticari araç kullanıcıları için kış lastiği uyarısı anlamını taşıyor. Bu noktada bazı kafa karışıklıklarını ve yanlış bilinenleri ortadan kaldırmak gerekiyor. 13 Kasım 2014, Perşembe
- İşbirlikleri Tam Gaz Otomotiv sektörü dünyanın en hareketli sektörlerinden biri. Sürekli yenilikler, değişimler, gelişimler söz konusu. 31 Temmuz 2014, Perşembe